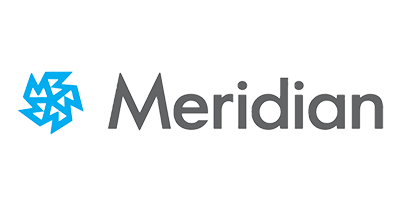
Meridian est un leader dans le domaine du moulage sous pression du magnésium. Avec des installations de fabrication situées sur des sites clés au Canada, aux États-Unis, au Royaume-Uni, en Allemagne, en Chine et au Mexique, l’entreprise fournit aux équipementiers automobiles du monde entier des pièces moulées sous pression légères.
Parce que les FEO doivent commencer à suivre les pièces moulées dès le début de la chaîne d’approvisionnement, Meridian a dû trouver une solution pour mettre en œuvre la traçabilité directement dans l’usine de moulage.
Une usine de moulage sous pression est un environnement difficile pour tout équipement, et celle de Meridian ne fait pas exception. Sa température ambiante est non contrôlée et oscille entre 10 °C et 50 °C, et l’air est poussiéreux.
Ces conditions difficiles peuvent nuire aux lasers, entraîner des temps d’arrêt et réduire considérablement leur durée de vie. L’intégration est essentielle pour protéger le laser.
Meridian a intégré une gamme de machines de marquage Laserax dans ses installations. Ces machines comprennent des stations chargées manuellement et des convoyeurs automatisés. Toutes les solutions sont à l’épreuve des poussières et peuvent supporter de grandes différences de température.
Ils sont équipés de composants de qualité industrielle fournis par Laserax qui garantissent un entretien et des temps d’arrêt minimaux. Voici quelques exemples :
Même si les lasers nécessitent très peu d’entretien, cet entretien est essentiel dans les environnements difficiles. Dans le cas de Meridian, il doit être effectué chaque semaine.
L’équipe d’assistance de Laserax était là au début des opérations pour enseigner à l’équipe de l’atelier comment entretenir les appareils laser, dans le but de prévenir les temps d’arrêt et de maximiser la durée de vie des lasers.
Selon leur ingénieur de fabrication, ils ne prévoient pas de problèmes majeurs avec la machine s’ils poursuivent leur routine d’entretien hebdomadaire.
Meridian a acquis plusieurs stations rotatives chargées manuellement pour suivre une gamme de pièces moulées à la demande de son client FEO. Chaque chaîne possède sa propre station laser pour identifier et suivre les pièces moulées individuelles.
Les opérateurs chargent simplement les pièces moulées sur la station, les fixent en position sur un côté de la table rotative, puis lancent l’opération de marquage au laser. Lorsqu’une pièce de moulage est marquée, les opérateurs peuvent décharger une pièce de moulage précédemment marquée et en fixer une nouvelle en position de l’autre côté de la table. Cela les tient occupés et les aide à suivez le rythme des durées de cycle difficiles.
Après le succès des stations à chargement manuel, Meridian a acquis des machines de marquage laser pour sa ligne de convoyage de palettes dans une autre usine.
Ces machines sont entièrement automatisées, mais les opérateurs peuvent visualiser les opérations de marquage à travers une fenêtre protégée contre le laser et utiliser une IHM pour diagnostiquer le laser.
Les machines sont alimentées par des lasers à fibre optique 3D pour deux raisons : pour compenser les erreurs de positionnement de pièces dues à l’imprécision du convoyeur, et pour réduire la complexité mécanique en marquant à un angle de 45°.
La machine laser communique avec les caméras de vision situées plus tôt sur la ligne pour coder les renseignements d’inspection dans les identificateurs.
Les lasers de Meridian génèrent constamment des identificateurs à fort contraste sur leurs pièces moulées sous pression en magnésium, ce qui leur permet de répondre aux exigences de traçabilité des FEO.