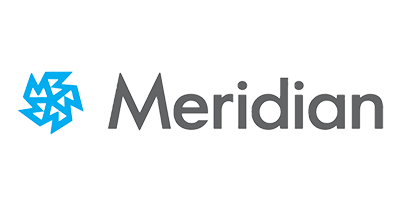
Meridian ist ein führendes Unternehmen auf dem Gebiet des Magnesiumdruckgusses. Mit Produktionsstätten an wichtigen Standorten in Kanada, den USA, Großbritannien, Deutschland, China und Mexiko beliefert das Unternehmen Automobilhersteller in aller Welt mit leichten Druckgussteilen.
Da OEMs die Gussteile schon früh in der Lieferkette verfolgen müssen, musste Meridian eine Lösung finden, um die Rückverfolgbarkeit direkt in der Gießerei zu implementieren.
Die Druckgießerei ist eine raue Umgebung für jede Ausrüstung, und die von Meridian ist keine Ausnahme. Ihre Umgebungstemperatur ist unkontrolliert und schwankt zwischen 10°C und 50°C. Zudem ist die Luft sehr staubhaltig.
Diese rauen Bedingungen können für Laser schädlich sein, zu Ausfallzeiten führen und ihre Lebensdauer drastisch verkürzen. Integration ist der Schlüssel zum Schutz des Lasers.
Meridian hat eine Reihe von Laserax-Beschriftungsmaschinen in seine Anlagen integriert. Zu diesen Maschinen gehören manuell bestückte Workstations und automatische Förderanlagen. Alle Lösungen sind staubdicht und können große Temperaturunterschiede aushalten.
Sie sind mit industrietauglichen Komponenten von Laserax ausgestattet, die dafür sorgen, dass Wartung und Ausfallzeiten auf ein Minimum reduziert werden. Einige davon sind:
Auch wenn Laser sehr wartungsarm sind, ist diese Wartung in rauen Umgebungen kritisch. Im Fall von Meridian muss sie wöchentlich durchgeführt werden.
Das Support-Team von Laserax war zu Beginn der Arbeiten vor Ort, um die Mitarbeiter in der Werkstatt in der Wartung der Lasermaschinen zur Vermeidung von Ausfallszeiten und der Verlängerung der Laser-Lebensdauer zu unterrichten.
Nach Angaben des Fertigungsingenieurs sind keine größeren Probleme mit der Maschine zu erwarten, wenn die wöchentliche Wartungsroutine beibehalten wird.
Meridian erwarb mehrere manuell bestückte Rotations-Workstations, um eine Reihe von Gussteilen auf Wunsch des OEM-Kunden zu prüfen. Jede Straße verfügt über eine eigene Laser-Workstation zur Identifizierung und Verfolgung einzelner Gussteile.
Die Bediener laden die Gussteile einfach in die Station, fixieren sie auf einer Seite eines Drehtisches und starten dann den Laserbeschriftungsvorgang. Während ein Gussteil markiert wird, können die Bediener ein zuvor markiertes Gussteil entladen und ein neues auf der anderen Seite des Tisches anbringen. Das beschäftigt sie und hilft ihnen, mit den schwierigen Zykluszeiten Schritt zu halten.
Nach dem Erfolg der manuell bestückten Workstations erwarb Meridian in einem anderen Werk Laserbeschriftungsgeräte für ihre Palettenförderanlage.
Diese Geräte sind vollautomatisch, aber die Bediener können die Markiervorgänge durch ein lasersicheres Fenster beobachten und den Laser über eine MMS diagnostizieren.
Die Geräte werden aus zwei Gründen mit 3D-Glasfaser-Lasern betrieben: zum einen, um Fehler bei der Positionierung der Teile aufgrund der Ungenauigkeit des Förderbands auszugleichen, und zum anderen, um die mechanische Komplexität durch die Markierung in einem 45°-Winkel zu verringern.
Das Lasergerät kommuniziert mit Bildverarbeitungskameras, die sich weiter vorne in der Straße befinden, um die Inspektionsinformationen in den Identifikatoren zu codieren.
Die Laser von Meridian erzeugen durchgängig kontrastreiche Kennzeichnungen auf ihren Magnesium-Druckgussteilen, wodurch sie die Anforderungen der OEMs an die Rückverfolgbarkeit erfüllen können.