Das schnellste Schweißverfahren
Beim Herstellen von Zelle-Sammelschiene-Verbindungen dauert das Ultraschalldrahtbonden in der Regel zwischen 500 und 1000 ms pro Schweißnaht. Das Laserschweißen ist viel schneller, weil es weniger und sanftere mechanische Bewegungen erfordert: Nur die ultraschnellen Spiegel im Laserkopf müssen bewegt werden, um den Laserstrahl zu positionieren. Dadurch wird die Positionierungszeit für jede Schweißnaht drastisch reduziert. Bei der Integration mit unseren Robotern kann die durchschnittliche Schweißzeit einschließlich der mechanischen Bewegungen zwischen den Zellen Werte unter 100 ms pro Zelle erreichen.
Zellentyp | Dicke der Sammelschiene | Zellendicke | Art der Schweißnaht | Abmessungen der Schweißnaht | Laserleistung | Widerstand (µΩ) | Schertest (N) | Zeit (ms) | Eindringtiefe (µm) |
---|
21700 zylindrisch | 250 µm Al 1100 | 500 µm vernickelter Stahl | Pluspol | Spirale 2,4 mm | 450 W | 5 | 195 | 40 | 100–150 |
21700 zylindrisch | 250 µm Al 1100 | 300 µm vernickelter Stahl | Minuspol | S-Form 3,6 x 0,5 mm | 450 W | 5 | 150 | 40 | 100–150 |
4680 zylindrisch | 600 µm Al 1050 | 0,8 mm Al 1100 | Pluspol | Spirale 4 mm | 750 W | 4 | 650 | 85 | 100–150 |
4680 zylindrisch | 600 µm Al 1050 | 0,8 µm vernickelter Stahl | Minuspol | Spirale 4 mm | 750 W | 1,2 | 800 | 85 | 100–150 |
Prismatisch | 2,32 mm Al | 1,62 mm Al | Pluspol | Spirale 7 x 5 mm | 2.000 W | 3,5 | 2.200 | 283 | 300–500 |
Prismatisch | 2,32 mm Al | 1,62 mm vernickeltes Kupfer | Minuspol | Spirale 7 x 5 mm | 2.000 W | 4 | 2.500 | 236 | 300–500 |
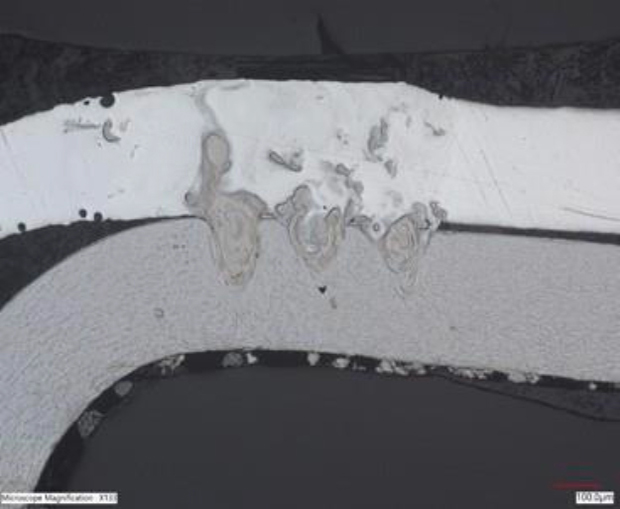
Querschnittsansicht des Laserschweißens von Sammelschienen – Negative Klemme (Mikroskopaufnahme)
- 250 um Al auf 300 um vernickeltem Stahl
- Form: S-Form
- Abstand: 200 um
- Abmessungen: 3,6 x 0,5 mm
- Geschwindigkeit: 500 mm/s
- Kein Hilfsgas
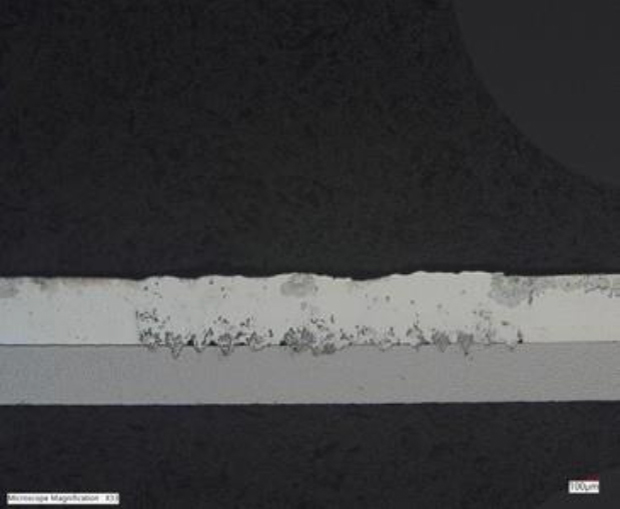
Querschnittsansicht des Laserschweißens von Sammelschienen – Negative Klemme (Mikroskopaufnahme)
- 600 um Al auf 500 um vernickeltem Stahl
- Form: Spirale
- Abstand: 200 um
- Abmessungen: 4 mm
- Geschwindigkeit: 700 mm/s
- Kein Hilfsgas
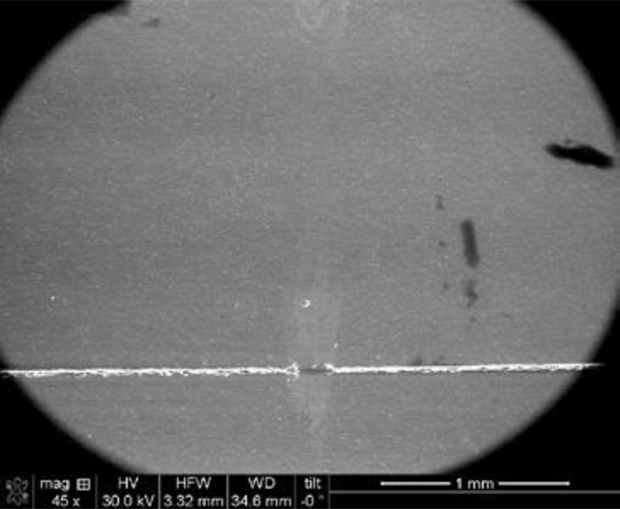
Querschnittsansicht des Laserschweißens von Sammelschienen (REM-Bild)
- 2,32 mm Al auf 1,62 mm Al
- Geschwindigkeit: 230 mm/s
- 51/min Argon-Hilfsgas
Schweißnahtüberwachung in Echtzeit zur Erkennung schlechter Schweißnähte
Geräte zur Laserschweißüberwachung (LWM) können eingesetzt werden, um schlechte Schweißnähte während des Laserschweißens in Echtzeit zu erkennen. So wird sichergestellt, dass jede einzelne Schweißnaht in der Batterie einwandfrei ist und dass fehlerhafte Schweißnähte sofort nachgearbeitet werden.
Optische Sensoren, die in den Laser eingebaut sind, verwenden die von der Schweißnaht reflektierte und emittierte Strahlung, um festzustellen, ob die Schweißnaht gut ist. Sie können verschiedene Arten von Schweißfehlern wie Spalten oder Verunreinigungen erkennen.
- Jede Zeile steht für eine Wellenlänge, die vom LWM erfasst wird (Plasma, Wärme, Laserrückstrahlung).
- Die blaue Linie in jeder Zeile stellt die in Echtzeit verfolgten abgestrahlten, reflektierten Lichtsignale für die aktuelle Schweißung dar.
- Die beiden grünen Linien in jeder Zeile stellen die ± Akzeptanzgrenzen für die Wellenlänger zu einem bestimmten Zeitpunkt dar.
- Blaue Linien, die für eine bestimmte Zeit über die grünen Akzeptanzgrenzen hinausgehen, können mit Schweißfehlern in Verbindung stehen.
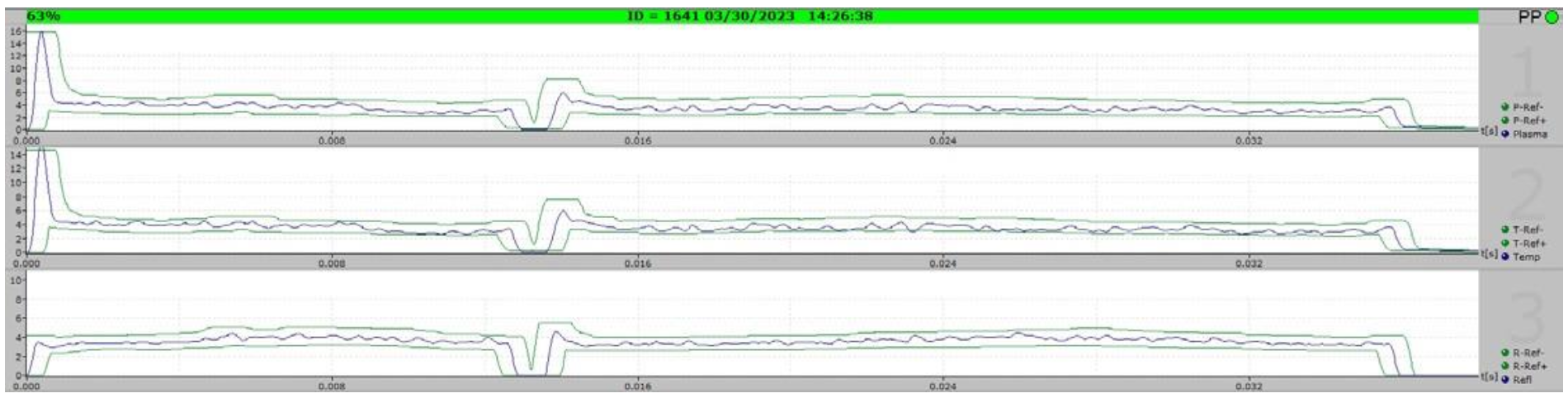
Revolutionierung der Effizienz
Aufgrund unserer höheren Schweißgeschwindigkeit kann ein einziges Laserschweißgerät problemlos wie 10 Ultraschall-Drahtbonder arbeiten. Dadurch wird die Anzahl der in den Produktionsstätten benötigten Geräte minimiert, wodurch Sie:
- Quadratmeter sparen
- Energie sparen
- Den Wartungsaufwand verringern
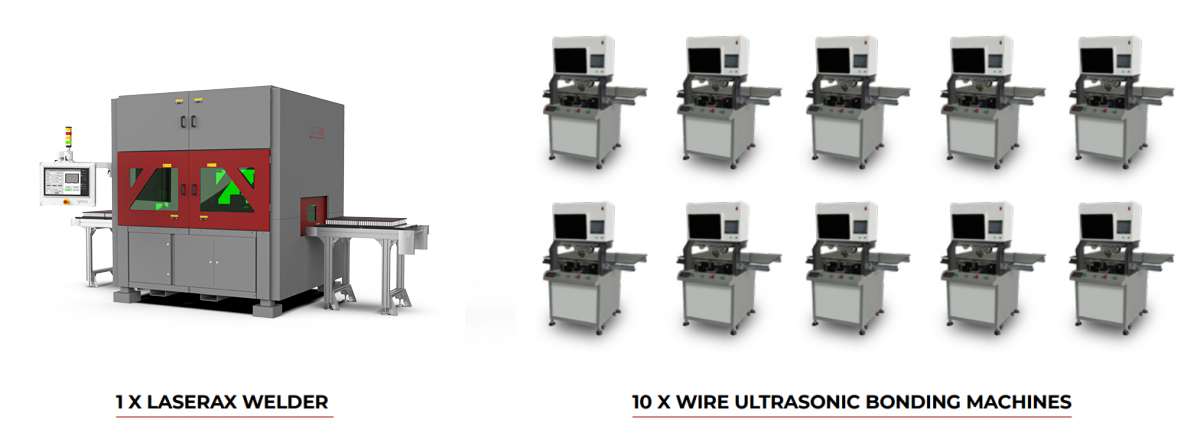
Zylindrische Zellen: Von 4 Schweißnähten zu 2 Schweißnähten
Während beim Ultraschalldrahtbonden in der Regel vier Schweißnähte pro Zelle erforderlich sind, benötigt das Laserschweißen nur zwei. Dies bietet mehrere Vorteile:
- Eine größere Kontaktfläche
- Halb so viele potenzielle Fehlerquellen
- Eine Schweißnaht trägt den gesamten Strom (höherer Strom pro Schweißnaht)
- Weniger mechanische Belastung für das Modul
- Geringerer Widerstand (weniger Wärme und elektrischer Verlust)
- Bessere Stromverteilung
- Bessere Wärmeübertragung von den Zellen zu den Sammelschienenleitern
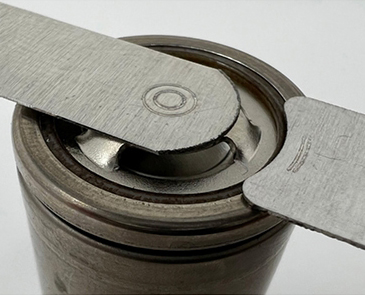
2 Schweißnähte pro Zelle (anpassbares Schweißmuster)
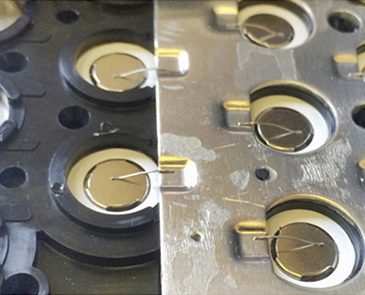
Ultraschalldrahtbonden mit 2 Drähten pro Zelle (oben und unten) und 2 kleinen Schweißnähten
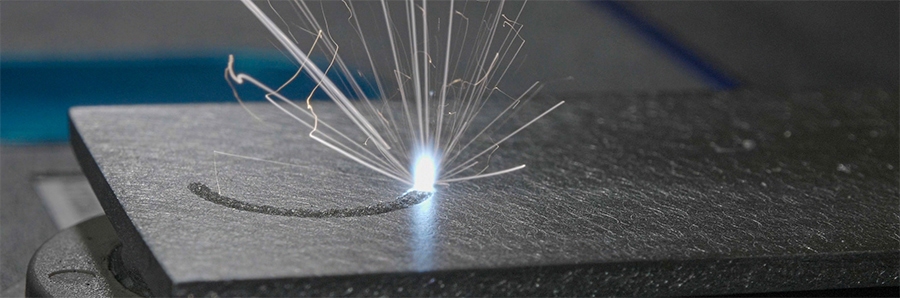