最速の溶接プロセス
セルとバスバーを接合する場合、超音波ワイヤーボンディングは通常、溶接1回あたり500~1000 msを要します。レーザー溶接は機械的な動きが少なく、よりスムーズなので非常に高速です。レーザービームを位置決めするために移動する必要があるのは、レーザーヘッドに配置された超高速ミラーだけです。このため、各溶接の位置決め時間が大幅に短縮されます。当社のロボットと組み合わせると、セル間の機械的な移動を含めた平均溶接時間は、1セルあたり100 ms以下に達します。
セルタイプ | バスバーの厚み | 電池の厚み | 接合タイプ | 接合寸法 | レーザー出力 | 抵抗(µΩ) | せん断テスト(N) | 時間(ms) | 浸透深さ(µm) |
---|
21700円筒型 | 250 µm Al 1100 | 500 µmニッケルメッキ鋼 | 正極 | スパイラル2.4 mm | 450W | 5 | 195 | 40 | 100~150 |
21700円筒型 | 250 µm Al 1100 | 300 µmニッケルメッキ鋼 | 負極 | Sシェイプ 3.6 x 0.5 mm | 450W | 5 | 150 | 40 | 100~150 |
4680円筒型 | 600 µm Al 1050 | 0.8 mm Al 1100 | 正極 | スパイラル4 mm | 750W | 4 | 650 | 85 | 100~150 |
4680円筒型 | 600 µm Al 1050 | 0.8 µmニッケルメッキ鋼 | 負極 | スパイラル4 mm | 750W | 1.2 | 800 | 85 | 100~150 |
プリズム状 | 2.32 mmアルミニウム | 1.62 mmアルミニウム | 正極 | スパイラル7 x 5 mm | 2000W | 3.5 | 2200 | 283 | 300~500 |
プリズム状 | 2.32 mmアルミニウム | 1.62 mmニッケルメッキ銅 | 負極 | スパイラル7 x 5 mm | 2000W | 4 | 2500 | 236 | 300~500 |
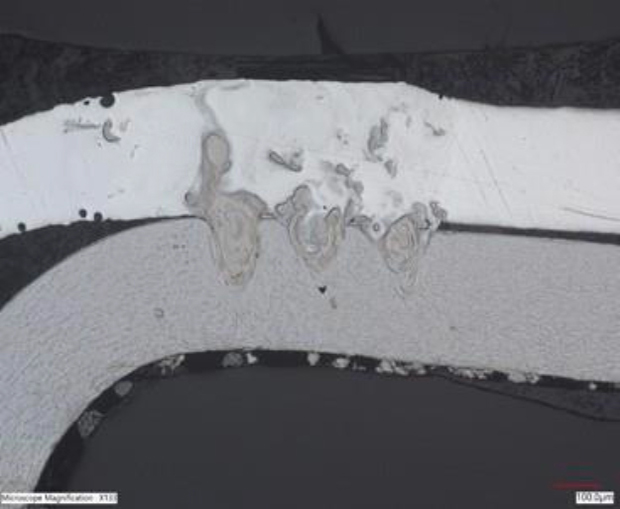
バスバーレーザー溶接の断面図 - 負極タブ(顕微鏡画像)
- 300 umニッケルメッキ鋼上に250 umアルミニウム
- シェイプ:Sシェイプ
- ピッチ:200 mm
- 寸法:3.6 x 0.5 mm
- 速度:500 mm/s
- アシストガスなし
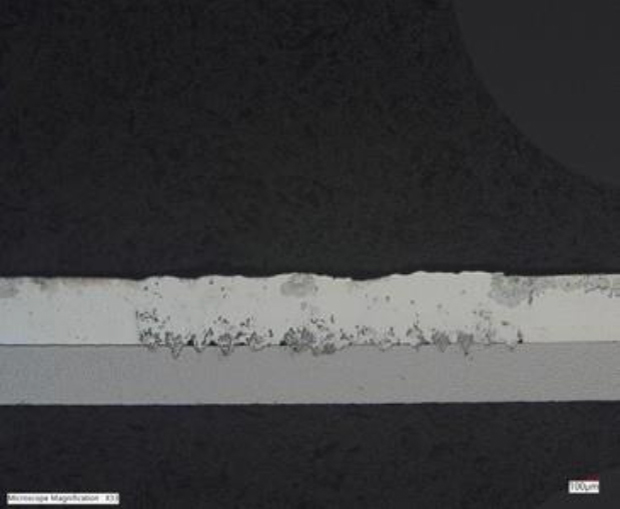
バスバーレーザー溶接の断面図 - 負極タブ(顕微鏡画像)
- 500 umニッケルメッキ鋼上に600 umアルミニウム
- シェイプ:スパイラル
- ピッチ:200 mm
- 寸法:4 mm
- 速度:700 mm/s
- アシストガスなし
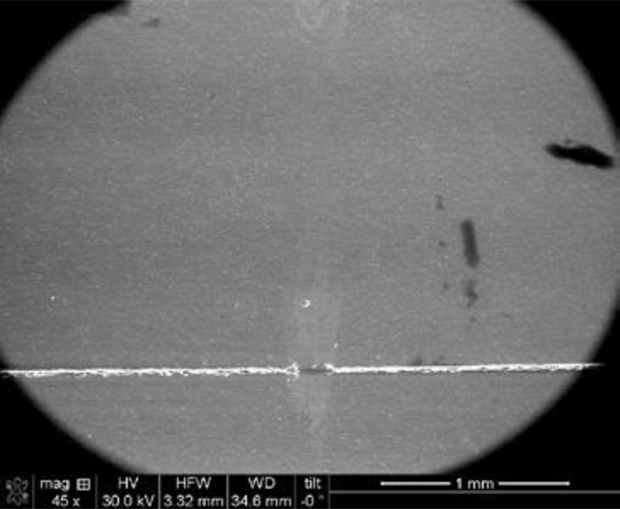
バスバーレーザー溶接の断面図(SEM画像)
- 1.62 mmアルミニウム上に2.32 mm Al
- 速度:230 mm/s
- 51/minアルゴンアシストガス
接合部の不良を検出するリアルタイムモニタリング
レーザー溶接モニタリング(LWM)デバイスを使用すると、レーザー溶接中に接合部の不良をリアルタイムに検出することができます。これにより、バッテリー内のすべての接合部が良好であることが保証され、接合部に不良があった場合はすぐにやり直すことができます。
レーザーに取り付けられた光センサーは、溶接によって反射および放射された放射線を利用して接合部の状態を判断します。これらの装置を利用すると、ギャップや汚染など、さまざまな接合部の不良を検出できます。
- 各行は、LWM(プラズマ、熱、レーザー反射)によって追跡される波長を表します
- 各行の青い線は、現在の溶接でリアルタイム追跡している放射反射光信号を表します
- 各行の2本の緑色の線は、任意の時点における波長の±許容限界を表します
- 一定期間にわたって緑色の許容限界を超える青い線は、接合部の不良に関連付けられる可能性があります
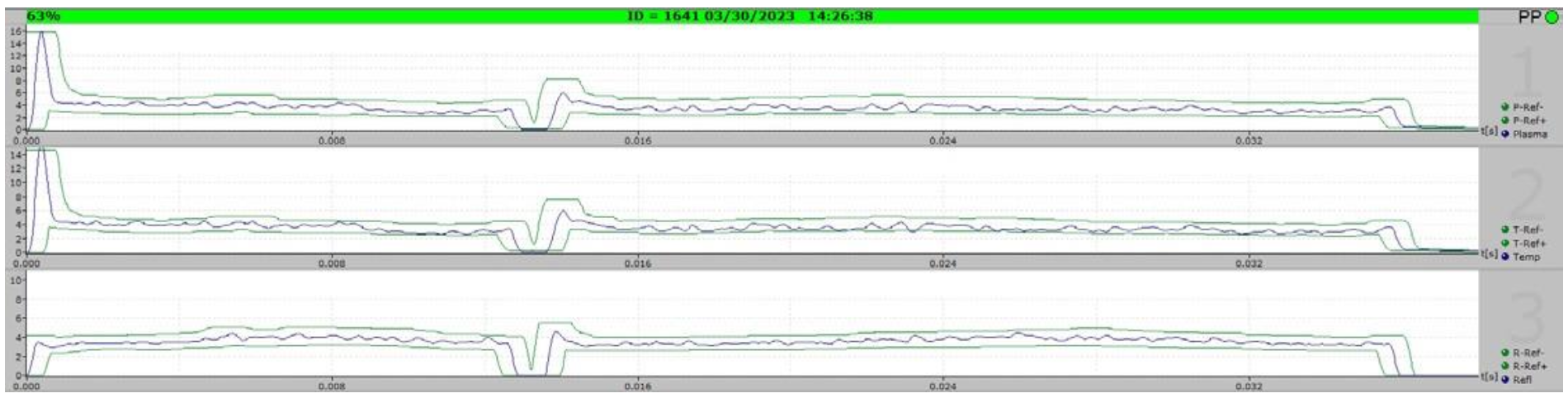
革命的な効率性
溶接速度が速いため、当社の単一レーザー溶接機は10台分の超音波ワイヤーボンディング装置を使用しているように簡単に作業を行うことができます。そのため、生産施設で必要なマシンの数が最小限に抑えられ、次のことが可能になります。
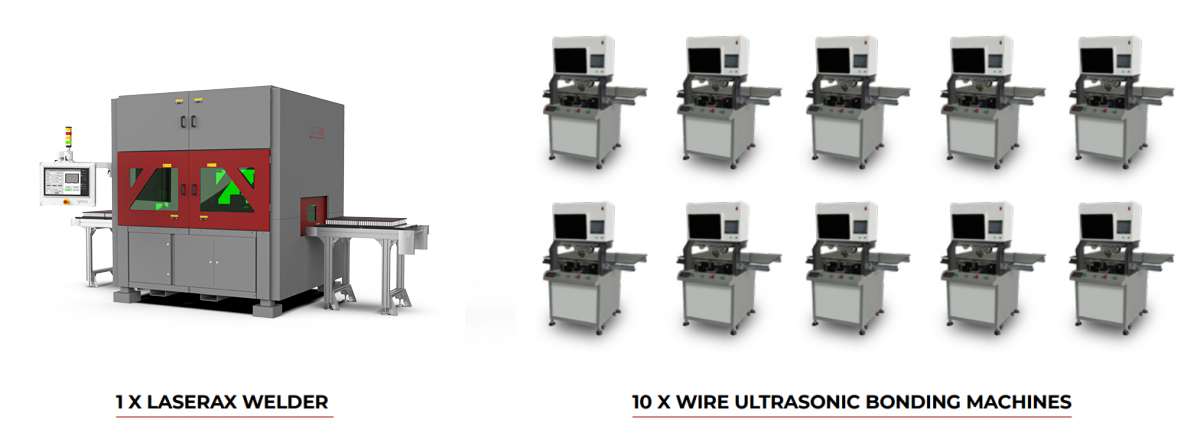
円筒型電池:溶接4回から2回
超音波ワイヤーボンディングでは通常、セルあたり4回の溶接が必要であるのに対し、レーザー溶接では2回のみです。これにはメリットがいくつかあります。
- 広範囲の接地面積
- 潜在的な不具合ポイントの半減
- 1回の溶接ですべての電流が流れる(溶接あたりの電流が高くなる)
- モジュールに伝達される機械的応力の減少
- より少ない抵抗力(熱損失・電気損失の低減)
- より良い電流供給
- セルからバスバー伝導体へのより良い熱伝達
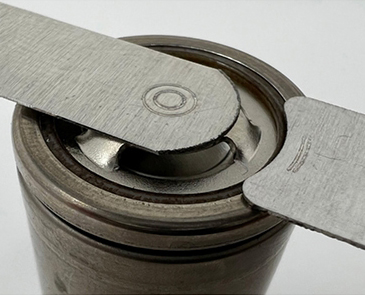
セルあたり2箇所の溶接(カスタマイズ可能な溶接パターン)
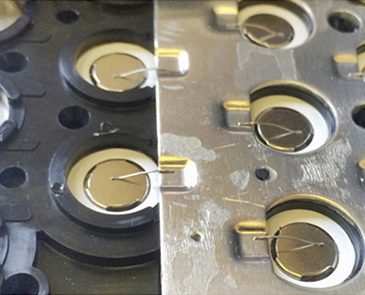
セルあたり2本のワイヤー(上下)と2つの小さな溶接による超音波ワイヤーボンディング
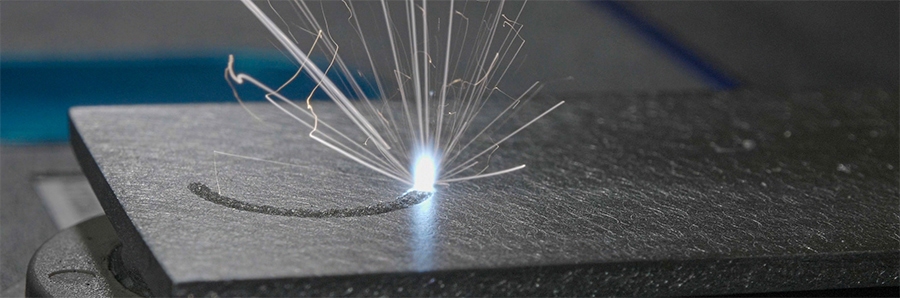