Cleaning For Ultrasonic Bonding: 99.99% Good Yield
In battery packs, there are hundreds or even thousands of welds on the cells and structure. Busbars, cell tabs, and other various electrical connections are all critical for the good operation of the battery. Laser cleaning guarantees that every single ultrasonic weld is perfect, optimizing the quality of the electrical contact and the overall weld strength.
Laser Cleaning Times For Different Number Of Cells
| Cycle Time (Sec) |
---|
Number of cells | 30w | 50w | 100w | 200w |
---|
120 | 11.5‑13.0 | 8.5‑10.0 | 6.2‑7.7 | 5.1‑6.6 |
240 | 23.1‑26.1 | 17.0‑20.0 | 12.4‑15.4 | 10.1‑13.1 |
480 | 46.1‑52.1 | 34.0‑40.0 | 24.8‑30.8 | 20.3‑26.3 |
960 | 92.2‑104.2 | 67.9‑79.9 | 49.7‑61.7 | 40.6‑52.6 |
For each range, the longer times include the scanner repositioning.
Water Contact Angle Test Results
The water contact angle is a standard, proven test to validate surface cleanliness. Our tests demonstrate outstanding cleaning results.

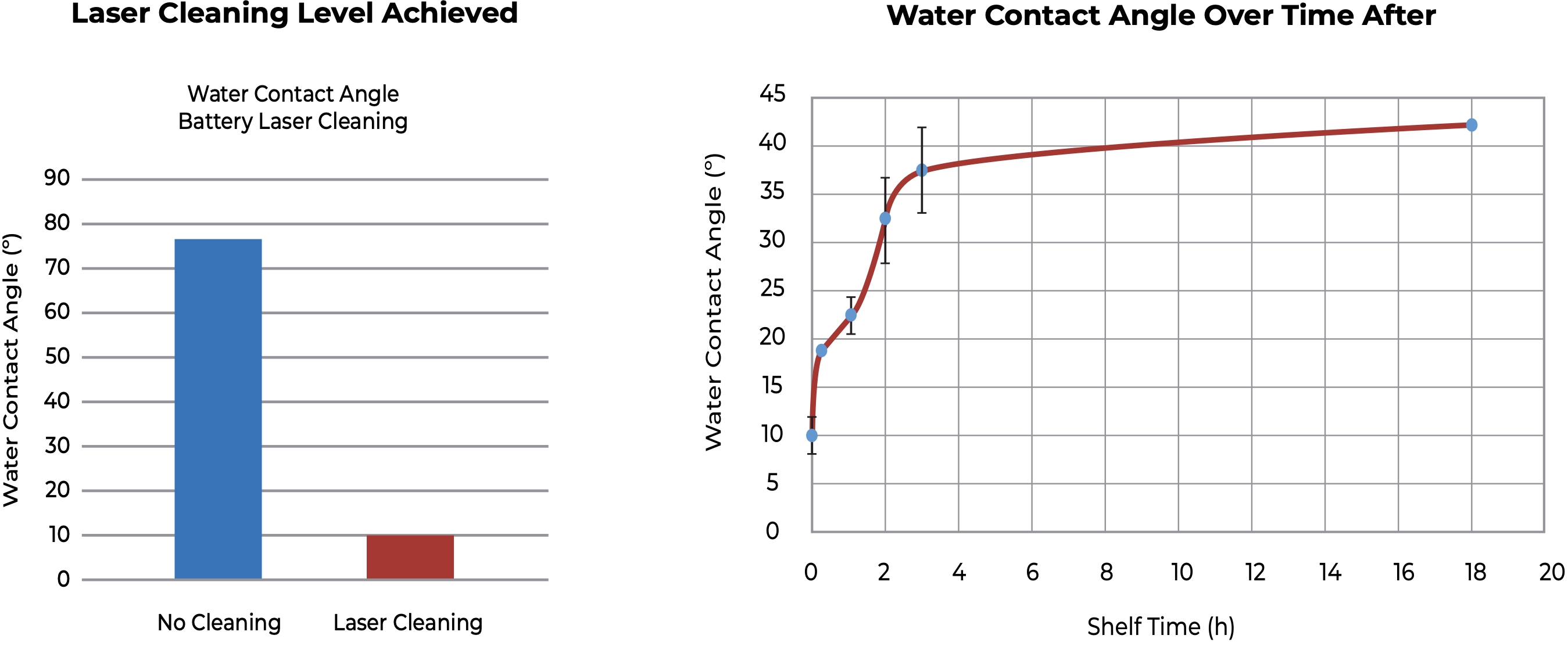
Cleaning To Improve Weld Monitoring Stability
Dynamic Laser Weld Monitoring (LWM) is used in battery production lines to ensure every single weld in the battery is good. These devices use reflected and emitted radiation from the weld to determine if the weld is good. They can detect different types of weld defects such as gap or contamination.
Laser welding is much less sensitive to contamination than ultrasonic bonding, but surface residues of varying thickness (such as oil and oxide) can still generate different signals that lead to false negatives, where a weld defect is detected where none exists. Laser cleaning of cell tabs before laser welding has been shown to not only help produce good welds every time, but also significantly reduce the amount of false negatives reported by LWM devices.
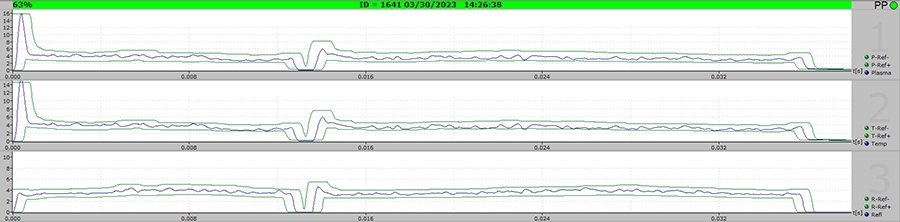
Laser Cleaning Effect On The Electrical Resistance Of Welds
Laserax performed tests to show effects of laser cleaning on the electrical resistance of welds. We used a 100W pulsed fiber laser to clean surfaces before tab-to-busbar welding. Laser cleaning guarantees the best yield strength when welding. It delivers 2x better overall process capabilities (Cpk) when compared to alternative cleaning methods. Higher quality equals less or no rework to optimize overall process throughput.
- Minimal heat loss
- Improved battery life
- Better thermal management
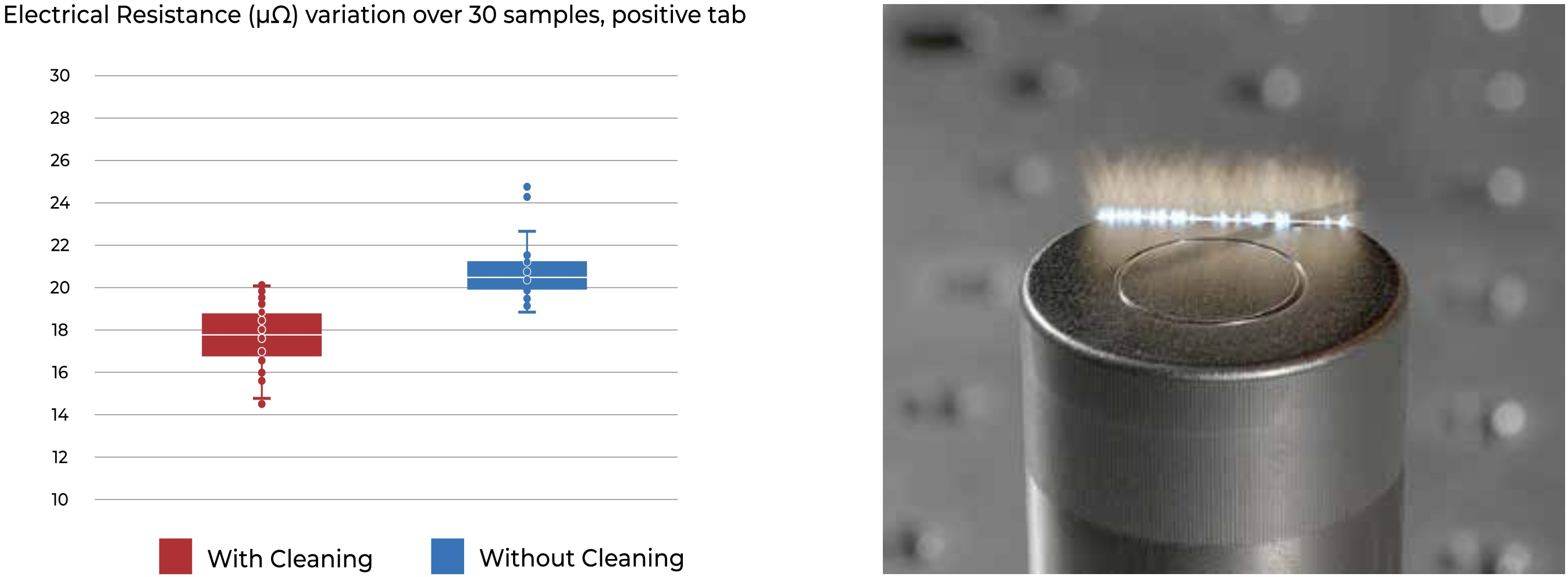