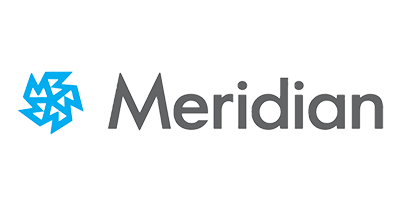
Meridian is a leader in magnesium die castings. With manufacturing facilities at key locations in Canada, the USA, the UK, Germany, China, and Mexico, they provide automotive OEMs all around the world with lightweight die castings.
Because OEMs need to start tracking castings early in the supply chain, Meridian had to find a solution to implement traceability directly in the casting plant.
The die casting plant is a harsh environment for any equipment, and Meridian’s is no exception. Their environment temperature is uncontrolled and oscillates between 10°C and 50°C, and the air is dusty.
These harsh conditions can be harmful for lasers, lead to downtimes, and drastically diminish their lifespan. Integration is key to protect the laser.
Meridian has integrated a range of Laserax marking machines in their facilities. These machines include manually loaded workstations and automated conveyor machines. All solutions are dustproof and can sustain large temperature differences.
They are equipped with industrial grade components provided by Laserax that make sure maintenance and downtimes are kept to a minimum. Some of these include:
Even though lasers require very low maintenance, this maintenance is critical in harsh environments. In Meridian’s case, it needs to be performed weekly.
Laserax’s support team was there during the beginning of the operations to teach the shopfloor crew how to maintain the laser machines, with the goal to prevent downtimes and maximize the lasers’ lifespan.
According to their manufacturing engineer, they don’t foresee any major problems with the machine if they continue their weekly maintenance routine.
Meridian acquired several manually loaded rotary workstations to track a range of castings as requested by their OEM client. Each line has its own laser workstation to identify and track individual castings.
Operators simply load the castings onto the station, fix them into position onto one side of a rotary table, then launch the laser marking operation. While a casting is marked, operators can unload a previously marked casting and fix a new one into position on the other side of the table. This keeps them busy and helps keep up with challenging cycle times.
Following the success of the manually loaded workstations, Meridian acquired conveyor laser marking machines for their pallet conveyor line in a different plant.
These machines are fully automated, but operators can view the marking operations through a laser-safe window and use an HMI to diagnose the laser.
The machines are powered by 3D fiber lasers for two reasons: to compensate for part positioning errors due to the conveyor’s imprecision, and to reduce mechanical complexity by marking at a 45° angle.
The laser machine communicates with vision cameras located earlier on the line to encode the inspection information in the identifiers.
Meridian’s lasers consistently generate high-contrast identifiers on their magnesium die castings, allowing them to meet OEM traceability requirements.